The Premium Hot Standby redundancy offer, which is
compatible with Unity Pro software, ensures continuity of operation
for an automation system based on a Modicon Premium platform in the
event of failure of:
It is based on the “Primary/Standby” redundancy
principle, with complete redundancy of the main processing and
communication functions, the use of shared I/O on the Ethernet
TCP/IP network, a Modbus link and/or redundancy of in-rack I/O
(single-rack confi guration only).
Premium Hot Standby redundant architectures offer an
ideal solution for availability requirements when changeover time is
not critical. They are designed for processes which can tolerate a
lack of control on the part of the Premium PLC lasting up to one
second (average changeover time from the “Primary” unit to the
“Standby” unit and for updating shared I/O on Ethernet).
They can meet all availability requirements when the
purpose of the PLC is to monitor and control an installation in
continuous operation, signal incidents to a control station, and
transmit command instructions from the supervision manager to
various locations on an extensive site.
Example areas of application:
-
Centralized technical management of a public
facility (tunnel, airport, signals, etc.)
-
Control/monitoring of a water treatment or
distribution station
-
Electrical technical management
-
Hydroelectric power production
-
etc.
Principle
At the centre of the system, there are two Modicon
Premium single-rack configurations called the “Primary” PLC and the
“Standby” PLC. Their hardware and software configurations are
identical (i.e. identical modules in each rack). The offer comprises
two processor models (TSX H57 24M and TSX H57 44M) designed specifically
for Hot Standby architectures with Unity Pro software (version u
3.1). This dual processor configuration combines the functions of the
CPU and redundant coprocessor in the same unit.
The “Primary” PLC:
Executes the application program and manages the I/O,
which can take the form of:
-
Field devices on an Ethernet network managed by
the I/O Scanning service
-
Field devices on a Modbus master link
-
Sensors and actuators connected to Premium I/O
modules on bus X with single-rack configuration
Safeguards the transfer of all data via the “CPU
Sync” link to the “Standby” PLC at the start of every cycle.
In the event of a failure affecting the “Primary”
PLC, the standby system changes over automatically, whereby
execution of the application program and control of the I/O is
changed over to the “Standby” PLC within 1.5 cycles, with an
up-to-date data context.
An automatic mechanism for the assignment of “IP” and
“IP + 1” addresses changes the addresses of the Ethernet network
modules with the 2 Premium configurations which manage the field
devices. The same mechanism is used for “n” and “n + 1” slave
address assignments for Modbus link modules.
Once they have changed over, the “Standby” PLC
becomes the “Primary” PLC. Once the faulty PLC has been repaired and
reconnected to the standby system, it takes the role of the
“Standby” PLC.
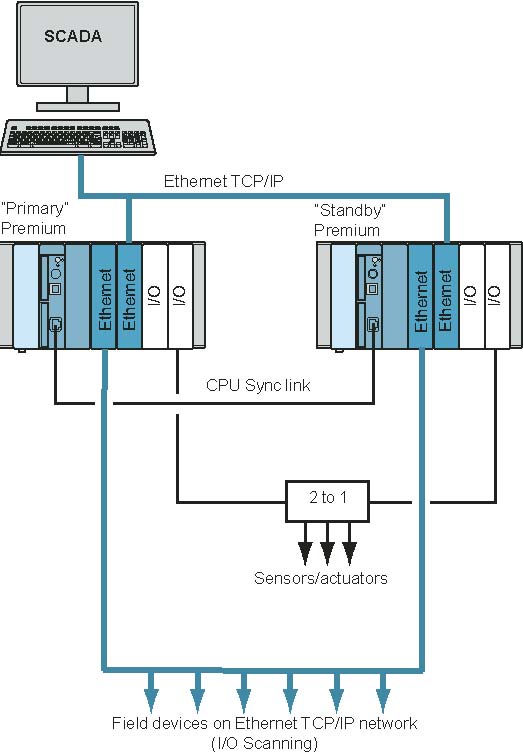
Architectures
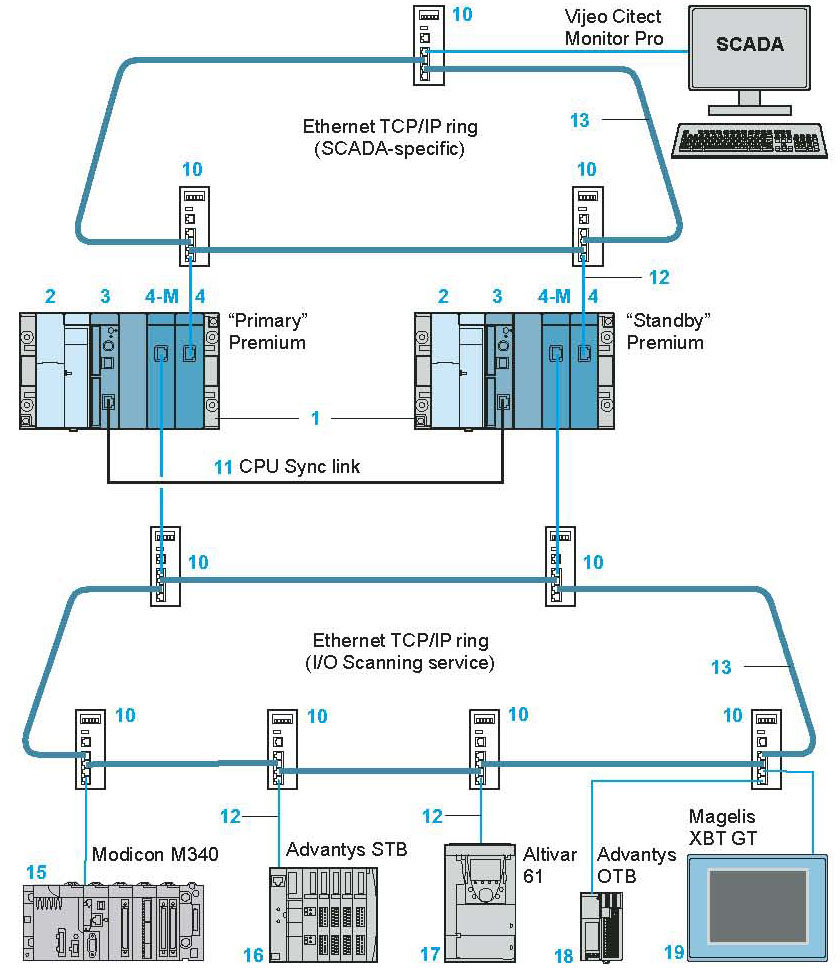
Typical architecture
In this type of architecture, the I/O system in Premium PLCs
equipped with a dedicated Hot Standby TSX H57 24M/44M processor is
defined by the distribution of field devices or equipment on the
Ethernet TCP/IP network. From an operational point of view, the
following devices or equipment are connected on the same Ethernet
TCP/IP network:
-
Client: Twido controller, Modicon PLC,
Magelis HMI, W@de remote management module, etc.
-
Modbus TCP server: Advantys OTB/Momentum
distributed I/O, Advantys STB I/O islands, Altivar variable
speed drives, Lexium servo drives, Inductel/Ositrack
identification systems, etc.
The Ethernet I/O Scanning
service enables client-server exchanges between a PLC and Ethernet
equipment communicating by means of the Modbus TCP protocol. This
service can be used to define up to 64 periodic read or write
exchanges in the form of a configuration, based on tables of (word
type) variables for target devices or equipment. The I/O Scanning
service is a function that is available as standard with TSX ETY
4103/5103 Ethernet network modules.
Elements for redundancy
-
6, 8 or 12-position non-extendable rack TSX
RKY
-
Power supply module TSX PSY pppM
-
Premium Hot Standby processor TSX H57
24M/44M
-
Ethernet TCP/IP network module TSX ETY
4103/5103
(version >= sv 4.0)
Ethernet TCP/IP ring shared elements
-
Modicon M340 automation
platform featuring processor with built-in Ethernet port BMXP34
2020/2030
-
Advantys STB modular
distributed I/O with network interface module STB NIP 2212
-
Altivar 61/71 variable
speed drive with communication card VW3 A3 310
-
Advantys OTB Optimum
distributed I/O with interface module OTB 1E0 DM9LP
-
Magelis XBT GT graphic
terminal with on-board Ethernet port XBT GT pp30/40
Other possible shared
elements:
—Advantys FTM, IP 67 modular I/O
—Momentum distributed I/O -TSX ETG 100/1000 gateway for connecting
Modbus devices
—W@de remote management modules (RTU), designed for water
applications TSX HEW 315/320/330
—Inductel/Ositrack identifi cation system XGK S1715503 and XGK
Z33ETH
—Lexium servo drives with communication card
AMO ETH 001V000 -Preventa XPS MF compact and modular safety PLCs
Ethernet wiring elements:
-
ConneXium managed switch
with 2, 4 or 8 10/100BASE-TX ports TCS ESM 0p3
-
CPU Sync link, copper
crossover cable 490 NTC 000
-
Copper straight-through
cable 490 NTW 000
-
Copper crossover cable 490
NTC 000
【打印】【返回代理產品列表】【返回頂部】 |